Skupina ČD / Zkušební stav VUZ: Fascinující ocelové město
Zkušební stav VUZ: Fascinující ocelové město
19.12.2019 – autor: JOSEF HOLEK
S Výzkumným Ústavem Železničním, dceřinou společností Českých drah, je vedoucí Jiří Soukup spjatý prakticky od dětství, kdy sledoval provoz zajímavých železničních vozidel na cerhenickém okruhu. Vystudoval dopravní fakultu, nastoupil do VUZ a před třemi roky se stal vedoucím Dynamického zkušebního stavu (DZS). Co dokážou specialisté vyzkoušet a jaké podmínky k tomu potřebují?
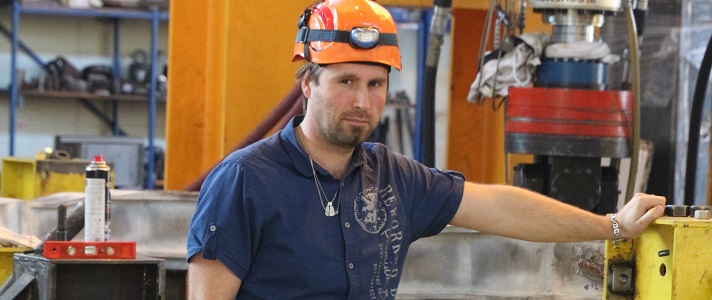
Železnice byla a je v rodině Jiřího Soukupa, vedoucího cerhenického Dynamického zkušebního stavu Výzkumného Ústavu Železničního, tématem číslo jedna. Už jeho otec byl specialistou a šéfem odboru správy VUZ a Jiří coby malý kluk miloval cerhenický okruh. Díval se na projíždějící vlaky, fascinovala ho doprava. Pozoroval lokomotivy i jednotky, které jinde nejezdily. „A také tu byl první počítač, který jsem viděl. Byla to dva-osm-šestka,“ zasmál se Jiří Soukup nad první vzpomínkou. Byl to začátek devadesátých let a další příjemné zážitky jen přibývaly.
Jeho další směřování předurčila až vysoká škola. „Mám obor Dopravní prostředky a kolejová vozidla na Dopravní fakultě Jana Pernera v Pardubicích.“ Pak se naskytla příležitost být vedoucím zkoušek na DZS VUZ a Soukup neváhal. To se psal rok 2007. „Díly, včetně rámů nebo náprav, zkoušíme podle různých specifikací a norem. Měl jsem pak na starosti celý projekt od A do Z. Pracoval jsem manuálně na stavu, připravoval technické zprávy. Dostal jsem se do reality, která byla úplně jiná než teorie ve skriptech. Používal jsem měřicí systémy, k nimž bylo vždy nutné doprogramovat uživatelské rozhraní v prostředí LabView na míru každé zkoušce. To vás nikde nenaučí. V hlavě mi utkvěl hned první projekt, kdy jsme zkoušeli rám podvozku pro italského zákazníka. Nic složitějšího jsem v životě neviděl. Neměli jsme s tím zkušenosti, a tak jsme se učili všichni.“
Natáhnout a roztrhnout
V roce 2016 se stal Soukup vedoucím celého DZS. Z haly, kde je stav instalovaný, tedy přesídlil do kanceláře a místo zkoušení začal jednat se zákazníky. „Jsme schopni vyzkoušet prakticky všechny části kolejových vozidel únavově, staticky i dynamicky. Dále jsme schopni měřit všechny možné veličiny, zejména na rámech podvozků a jejich částech včetně ložiskových komor a příčníků. Dále například provádíme únavové zkoušky kol, náprav nebo brzdových rozpor,“ vyjmenoval Soukup s tím, že VUZ má v portfoliu služeb i zkoušky infrastrukturních prvků. „Zkoušíme životnost pražců, kolejnic i jejich svarů,“ zmínil pár příkladů. Pro tyto účely jsou normou dané speciální únavové zkoušky, kdy se měří, kolik toho jednotlivé prvky vydrží. „Neděláme testy materiálu, ale simulujeme provozní odolnost,“ vysvětlil vedoucí.
V obří žluté hale, která je součástí cerhenického areálu VUZ, umí specialisté – zjednodušeně řečeno – roztrhnout i masivní kovové díly (háky či šroubovky). „Disponujeme pulsátorem, který umí vyvinout sílu až 250 tun. To už je možné roztrhnout prakticky cokoliv. Měříme tedy, při jaké síle a natažení díl povolí. Přitom zkoumáme i výchylku, takže dokážeme sestavit trhací diagramy daného materiálu.“ Do rukou se lidem okolo Jiřího Soukupa dostává nepřeberné množství různých prvků pro kolejová vozidla různé jakosti.
Nejdříve defektoskopie
Vyrobit kvalitní díl je dnes poměrně složité, byť se už v přípravné fázi využívá počítačová modelace. „Udělat například rám podvozku není nic jednoduchého. Vše se spočítá na počítačovém modelu, ale do analýzy nelze zakomponovat lidský um nebo kvalitu svaru. Výsledný rám se tedy od počítačového modelu mírně odlišuje. Naše zkoušky pak ověří finální produkt.“ Obecně vzato leckteří výrobci už mají systém vyladěný. Jde zejména o ty renomované. Dokázali si dát dohromady výsledky zkoušek a testů a daří se jim. Jiní se naopak ještě učí.
VUZ každý rok otestuje 3–4 rámy podvozků, desítky kol a další řadu prvků včetně systému upevnění kolejnic k pražcům. „Například nedávno jsme prováděli únavu železničního monoblokového kola pomocí resonančního stendu, tedy ohyb za rotace. Při této zkoušce je kolo připevněné k bloku a nad ním je nalisované ložisko s nevývažkem. Ložisko roztáčím a nevývažek, jak je umístěný na jedné straně, začne nápravu ohýbat více a více při stále vyšší rotaci. Když dosáhnu určité meze, ustálím rotaci. Třeba na 16 otáčkách za sekundu. Já pak sleduji mechanické napětí, které proces vyvodí na kole. To kolo musí vydržet deset milionů na určité hladině namáhání cyklů. Zkouška trvala zhruba osm dní, nonstop,“ zmínil Soukup zajímavost.
Řádně natlakovaná hydraulika
Jak ale celý proces zkoušky vypadá? Nejdříve vše musí odpovídat dokumentaci. Následuje vstupní defektoskopie (NDT metodou, tj. nedestruktivním zkoušením), zda na výrobku nejsou už z výroby vady. Pokud existují, jsou označeny. Na řadu přijdou i tenzometry, snímače mechanického napětí a při specifikovaných stavech zatížení specialisté sledují chování rámu. „Měříme mechanické napětí. Z toho poté dovodíme, zda je vůbec nutné dávat kus na dynamickou zkoušku, zda má předpoklady ji vydržet. Dále je rám zatěžován dynamickým, většinou sinusovým zatížením. Jednoduše řečeno simulujeme jízdu vlaku při daných podmínkách. Například při průjezdu obloukem nebo výhybkou,“ popsal Jiří Soukup.
Takový rám ale při zkoušce stojí. Pracují však hydraulické válce, jež simulují síly, které na rám působí v reálném provozu. Válce jsou k rámu připojené a zatížení vnáší do předem určených míst. Celý proces nemá přesně dané časové předěly, zkoušky jsou různě dlouhé, záleží na složitosti konstrukce. Vždy se ale bavíme o rozmezí od dvou do čtyř měsíců. Nejtěžší rámy jsou pro lokomotivy, lehčí pro osobní vozy a nejlehčí je standardní, typizovaný rám Y25 pro nákladní vozy. „Nejtěžší jsou naopak třínápravové, lokomotivní. Těžké jsou nejen na zkoušení, ale i na váhu – jejich hmotnost se pohybuje okolo pěti tun,“ potvrdil Jiří Soukup.
Hlavní jsou fakta
„I když je zkouška dokončena v plném rozsahu nebo je ukončena dříve z důvodu například vzniku únavové trhliny, sepíše se v poslední fázi protokol o zkoušce. Není to ale konečná v celém procesu. Rám se musí schválit. Pokud napíšu protokol, že trhlina vznikla po X milionech cyklů, pouze konstatuji to, co se stalo. Na vyhodnocení už výrobce použije jiný certifikační orgán. My dáme jen číslo, fakta a víme, při kolika cyklech by trhlina vzniknout neměla, a když, tak jaké velikosti. Na kladný průchod při schvalování jsou sestavené normy, a pokud je například rám splní, může jít do světa,“ zhodnotil šéf zkušebního stavu.
Reálně to tedy v hale vypadá tak, že na jednom stavu je testován rám, vedle jsou zkoušeny systémy upevnění nebo samotná kola. „Máme systém čtyř hydraulických agregátů, které napájí necelou třicítku počítačem řízených válců. Ty mohu naskládat po celé hale a je na nich možné provádět různé druhy zkoušek. Teoreticky lze dělat až třicet zkoušek najednou,“ vyzdvihl Soukup. „Hydraulický, vysokotlaký okruh, který pohání válce, disponuje provozním tlakem 28 MPa,“ dodal technický údaj. Technologie se neustále vyvíjí a VUZ na ně dokáže reagovat. Často tak do inovací DZS investuje.
Důraz na bezpečnost
Podlahu v hale tvoří gigantická, odpružená železobetonová deska s upínacím polem. Proč? Při kmitání u zkoušek vznikají parazitní frekvence a tyto vlivy zatížení by měly negativní vliv na konstrukci celé stavby. Aby po čase hala nespadla, je nutné mít „pracovní plochu“ oddělenou. Když se ale testují ložiskové jednotky na speciálním zkušebním stavu, funguje opačný princip. Tento stav je odpružený proto, aby parazitní frekvence z ostatních probíhajících zkoušek neovlivňovaly výsledky testů těchto jednotek. „Necítíte to, ale při dlouhodobém počínání už by vibrace vliv mít mohly,“ řekl Soukup.
Během provozu zkoušek je také nastaveno určité bezpečnostní opatření přímo na elektrohydraulickém systému. Počítač kontinuálně hlídá veškeré měřené a řízené signály vstupující do zkoušky a porovnává je s limitními hodnotami, které pokud jsou překročeny z důvodu například vzniku praskliny na zkoušeném prvku, tak PC automaticky odstavuje přísun vysokotlakého oleje z hydraulických válců a vypíná zkoušku. V takovém případě systém posílá sdělení pracovníkům na mobilní telefon.
Konečná fáze, tedy doba, kdy má být zkoušený prvek instalován na určité vozidlo, vypadá různě. Když velcí výrobci začnou vyrábět vozidlo, dobře vědí, co budou potřebovat, jak mají jednotlivé díly zkonstruovat a vše například vyzkouší na hotovém stroji. Pokud vykazuje díl vady, upravuje se přímo. „Většinou to není tak, že by kompletní rám podvozku musel být vyhozen, pokud se něco stane během zkoušek, ale například stačí udělat nějaké drobné konstrukční úpravy, které problém vyřeší. Nicméně takový prvek musí projít znovu zkouškami,“ uzavřel Jiří Soukup.
Řekli o Jiřím Soukupovi
Zdeněk Malkovský, generální ředitel, VÚKV
Jiřího Soukupa znám díky únavovým zkouškám rámů podvozků kolejových vozidel. Ty vyžadují hlubokou znalost teorie únavové pevnosti i praktické dovednosti při využívání moderních elektrohydraulických zatěžovacích válců. Důležitá je i osobní zodpovědnost za správný průběh a objektivní hodnocení. V osobě Jiřího Soukupa je toto zaručeno, a proto s ním rád spolupracuji.
Daniel Los, vedoucí železničního zkušebního okruhu Cerhenice, VUZ
Jirku jsem poznal již při studiích na dopravní fakultě v Pardubicích, resp. jejím dislokovaném pracovišti v České Třebové. Jeho ročník byl výjimečný množstvím výborných studentů, kteří se později stali špičkami v oboru železniční dopravy, a Jirka rozhodně nebyl výjimkou. Považuji jej za jednoho z největších odborníků na statické a únavové zkoušky rozličných komponentů železničních vozidel v hale Dynamického zkušebního stavu.
Prof. Bohumil Culek, DF Jana Pernera, Univerzita Pardubice
Jiří Soukup patří k lidem, kteří zůstali ve své profesní dráze prakticky věrni tomu, co vystudovali. To je v racionalitě jeho působení v praxi na DZS VUZ a v přínosu pro celou společnost VUZ velké plus. Pod jeho vedením drží pracoviště DZS vysokou profesionální úroveň standardních zkušebnických činností. Akce, na kterých má pan Soukup podíl, vytvářejí předpoklad úspěšného kolaborativního výzkumu DZS VUZ i v dalších letech.
Miloš Klofanda, provozní ředitel zkušebnictví, VUZ
Jiří Soukup nastoupil do VUZ po ukončení VSD v roce 2007. Hned po nástupu byl zařazen do ZC Velim zkušebny Dynamického zkušebního stavu. Po zapracování se v krátké době stal vedoucím zkoušek a od roku 2010 byl zástupcem vedoucího, kde se průběžně seznamoval s úkoly a potřebami tohoto střediska. Vzhledem k dobrým referencím od našich klientů a výsledkům jeho práce byl v roce 2016 jmenován vedoucím Dynamického zkušebního stavu. Má velmi dobré odborné technické znalosti, je dobře jazykově vybavený a vnímá potřeby a úkoly, které jsou na něho kladeny.
Další články této rubriky
Pražské datové centrum se výrazně rozšířilo
8.3.2025 - Dceřiná společnost Českých drah ČD - Telematika v lednu dokončila a zkolaudovala už čtvrtý technologický sál svého hlavního datového centra v Praze 9. Díky investici ve výši několika desítek milionů korun se po sedmi letech od… »
Pokud budeme důsledně postupovat podle nařízení č. 402/2013, pak doba psaní předpisů „krví“ skončila
1.1.2025 - Železnice denně přepraví miliony cestujících i tuny zboží. S vysokými nároky na spolehlivost, bezpečnost a efektivitu je nezbytné pečlivě sledovat a řídit rizika, která by mohla ohrozit plynulost provozu nebo bezpečnost… »
Zajímavosti z provozu ČD Cargo na Liberecku
18.11.2024 - Letošní rok byl na Liberecku opět ve znamení rozsáhlé výlukové činnosti. V prvním pololetí byl rekonstruován podjezd pod libereckým nádražím s výrazným dopadem na nákladní dopravu. Ta mohla využívat pouze část staničních… »