Skupina ČD / Za pár měsíců zjistí, co se s vlakem stane za 30 let
Za pár měsíců zjistí, co se s vlakem stane za 30 let
26.5.2021 – autor: JOSEF HOLEK
Dynamické zkoušení komponentů je chloubou Výzkumného Ústavu Železničního. Zkoušky probíhají v hale cerhenického Zkušebního centra na zařízení, které se nazývá dynamický zkušební stav. Zde pracuje i mladý odborník VUZ Radek Stuchlík. Má na starosti například testování rámů podvozků. A zatímco laické veřejnosti by jeho práce připadala abstraktní, on se ve svém oboru vyzná vskutku dokonale.
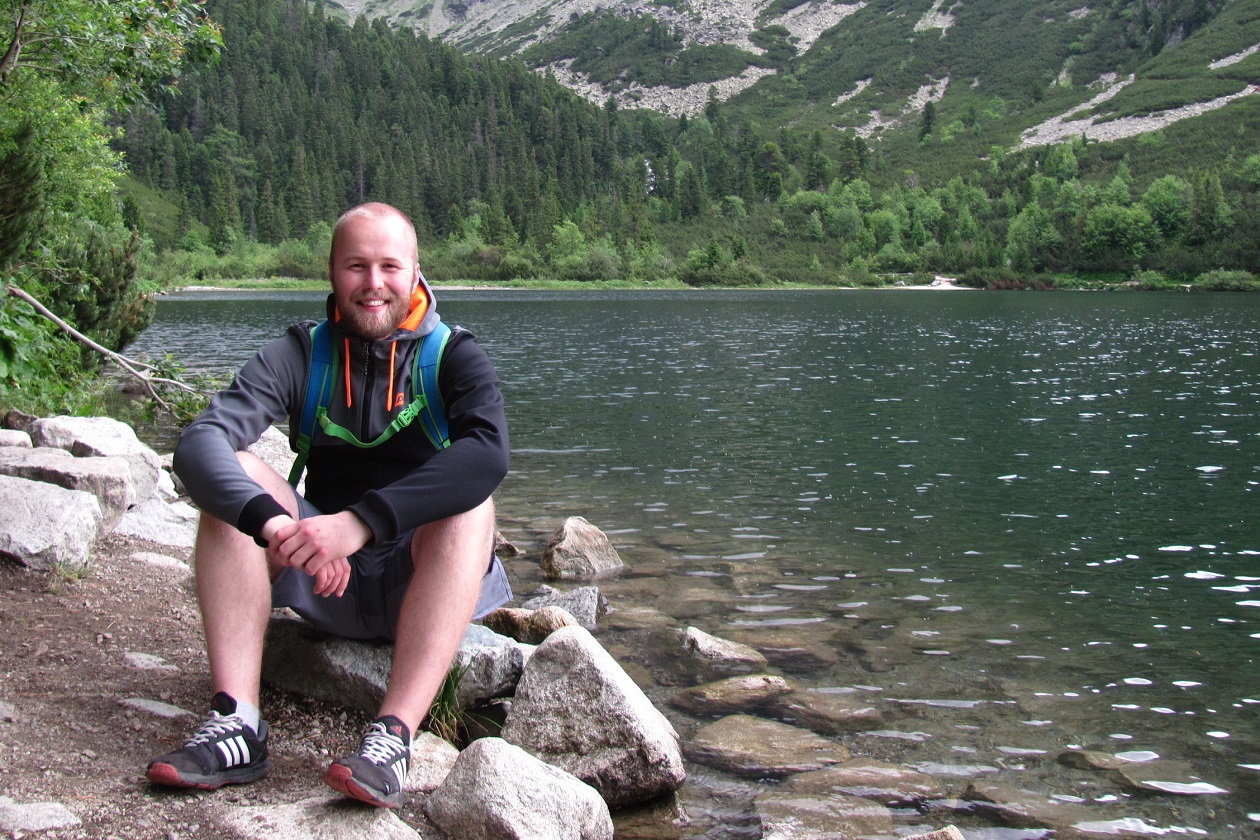
Radek Stuchlík, specialista VUZ, má železnici v krvi. Jeho otec je totiž strojvedoucí, a tak měl malý Radek k lokomotivám celkem blízko. Až na střední škole se lámal pomyslný chléb a student gymnázia přemýšlel i o studiu oboru zdravotnický záchranář. Nejspíše se projevil vliv maminky, zdravotní sestry.
Železnice ale přece jen zvítězila a Radek Stuchlík o pár let později promoval na Dopravní fakultě Jana Pernera Univerzity Pardubice po studiích oboru Dopravní prostředky – kolejová vozidla. V té době už měl za sebou i roční brigádnickou praxi právě ve VUZ. „Diplomka byla na téma Návrh zkušebního stavu pro zkoušky nápravových ložisek. Spolupracoval se mnou můj současný vedoucí, Jiří Soukup,“ upřesnil. VUZ totiž uvažoval o pořízení nového zařízení pro zkoušky nápravových ložisek. Radek Stuchlík, ještě v roli studenta, připravil návrh, ověřoval různé možnosti a zhodnotil stav staršího zařízení. Zpracoval tedy komparaci starého a nového zařízení včetně simulačních výpočtů na starém zařízení a navrhl nové. „Nové zařízení už funguje, částečně se vycházelo z mého návrhu, nicméně kompletní dokumentaci připravila externí firma, můj rukopis ale zařízení nese,“ podotkl specialista. „Pamatuji si i na svůj první projekt. Šlo o testování zařízení pro zvedání kolejnic. Už tehdy jsem komunikoval se zákazníkem, připravil projekt, provedl jej a vyhodnotil. Vše úspěšně,“ dodal.
Laboratoř VUZ neustále modernizujeme tak, aby odpovídala nejnovějším standardům a mohli jsme reagovat na požadavky zákazníků.Velký důraz dáváme na kvalitu práce tak, abychom naplnili očekávání zákazníků a ti se vraceli.
Příprava na týdny
Jako méně zkušený dostával za úkol provádět jednodušší zkoušky. Rukama mu procházely tlumiče a pružiny, upevnění kolejnic včetně kolejnic a upevňovadel. Za léta se ale vypracoval na zástupce vedoucího střediska a na starosti má aktuálně otestování rámu podvozku jedné elektrické jednotky. „Výrobce zasílá podvozek extra a u nás prochází zkouškou životnosti. Dokážeme za zhruba čtyři měsíce prověřit, zda vydrží 30 let,“ vysvětlil. Přípravné práce ale zaberou i dva měsíce.
Podvozek připraví pro zkušební stav a nechá ho řadu týdnů běžet prakticky nonstop. Než si ale odbyde těžko uvěřitelné hydraulické zatěžování s vysokou frekvencí, musí díl projít defektoskopickou kontrolou. Celý rám, respektive všechny svary Stuchlík a jeho tým prověří a udělá si vstupní obrázek. Dozví se tedy, v jakém stavu rám na začátku zkoušky je. Pokud existují výrobní vady, což se ostatně projeví záhy, musí specialisté kontrolovat jejich stav. Každá výrobní vada totiž může být iniciátorem nežádoucích únavových trhlin. K této zkoušce se používají drobné senzory napojené na počítač. Říká se jim tenzometry. „Aplikujeme je na rám podvozku před započetím statických zkoušek a nastavíme. Při zkouškách se měří mechanické napětí na konstrukci,“ popsal jednu z prvních fází. „Pomalým způsobem zkouším různé stavy zatížení podvozku. Tedy tak, jak mohou v reálném provozu nastat. Můžeme nastavit síly od skříně, brzd, od působení motorů na rám a dalších komponent, které jsou na podvozku připevněny.“
Oko nemá velkou šanci
Poté rám zaváže do stavu, kde na únavové zkoušce stráví řadu týdnů. Stav pak specialisté naprogramují tak, aby na podvozek působily síly předepsané výrobcem, tedy podle přesných norem a výpočtů. „U nás rám podstoupí 10 milionů cyklů, což znamená, že do dílu desetmilionkrát vnesu určitý balík sil a celý ten rám tak zatížím. Během této zkoušky ho mohu zatížit rychleji než při statických zkouškách. Dokážu sílu vnést 4x za sekundu,“ vypočítává Radek Stuchlík. Celá konstrukce se sice, zjednodušeně řečeno, výrazně třese, ale během dvou měsíců „natřásání“ dokáže ověřit celou živnost konstrukce.
Po měsících pod neustálým zatížením díl doputuje díl zpět na defektoskopickou zkoušku svarů, ze kterých Radek Stuchlík zjišťuje, kde se vyskytly trhliny. Pokud ji najde, hodnotí rozsah a místo, tedy zda ji našel na nosné konstrukci, nebo držáku potrubí. Okem jsou trhliny často nepostřehnutelné, ale existují i takové, které při bližším zkoumání najdete. Defektoskopie a její nástroje jsou tedy daleko přesnější. Kolega následně zhodnotí, zda má trhlina vliv na provozní bezpečnost, respektive jak je vliv velký. „Otázku, zda je velikost trhliny přípustná nebo nepřípustná, řeší příslušná norma. Vliv na provozní bezpečnost řeší schvalovatel – Kancelář autorizované osoby – spolu s výrobcem.“ Většina podvozků projde a po skončení zkoušky se trhliny nevyskytují, nicméně občas se najdou kusy, jeden dva do roka, které si musí zkoušku zopakovat. Výrobce je ještě před tím musí modifikovat.
V každém případě ale nastoupí úřední šiml. Radek Stuchlík musí sepsat protokol, finálním výstupem je akreditovaný protokol nebo technická zpráva. „Pokud výrobce usiluje o schválení pro provoz u dané komponenty, obrátí se například na naši Kancelář autorizované osoby a ta vydá certifikát o tom, že díl splňuje veškeré podmínky. Producent pak může usilovat o schválení provoz u nás i v Evropě,“ připomněl další dějství.
Testují vše
Co se týče kvality, existují výrobci, kteří rámy na stavu VUZ zkouší a vždy projdou. Nejčastěji v Cerhenicích testují nejrozšířenější typ podvozku pro nákladní vozy Y 25. Jen v letošním roce by bránu Zkušebního centra měly opustit dva takové. Rozhodně to však neznamená, že by se na DZS testovaly jen rámy podvozků nákladních vozů. Zkoušejí se zde rámy všech vozů kolejových vozidel včetně tramvají a metra, i složitější celky, jako je zkouška rámu podvozku s namontovaným příčníkem. „Zrovna loni jsme otestovali třínápravové podvozky pro jednu lokomotivu,“ vzpomněl Radek Stuchlík. „Máme zkoušky zažité, například ty s Y 25. Nicméně s každou další stojíme před novou výzvou.“
VUZ poskytuje služby i v oboru částí silničních vozidel, infrastruktury a dalších strojírenských oblastí. Zákazníci VUZ jsou z celé Evropy i blízkého a dálného Východu. Nejvíce produktů u nás však testují evropští producenti. „Za rok zvládneme otestovat zhruba 5 rámů. DZS ale zvládne odvést daleko více práce na vyšším počtu dílů ŽKV. Bývají mezi nimi i komponenty pro DPOV.
Další články této rubriky
Pražské datové centrum se výrazně rozšířilo
8.3.2025 - Dceřiná společnost Českých drah ČD - Telematika v lednu dokončila a zkolaudovala už čtvrtý technologický sál svého hlavního datového centra v Praze 9. Díky investici ve výši několika desítek milionů korun se po sedmi letech od… »
Pokud budeme důsledně postupovat podle nařízení č. 402/2013, pak doba psaní předpisů „krví“ skončila
1.1.2025 - Železnice denně přepraví miliony cestujících i tuny zboží. S vysokými nároky na spolehlivost, bezpečnost a efektivitu je nezbytné pečlivě sledovat a řídit rizika, která by mohla ohrozit plynulost provozu nebo bezpečnost… »
Zajímavosti z provozu ČD Cargo na Liberecku
18.11.2024 - Letošní rok byl na Liberecku opět ve znamení rozsáhlé výlukové činnosti. V prvním pololetí byl rekonstruován podjezd pod libereckým nádražím s výrazným dopadem na nákladní dopravu. Ta mohla využívat pouze část staničních… »